Product Recalls, Mass Torts and Class Action Claims
Learn If You May Be Eligible To Receive Compensation
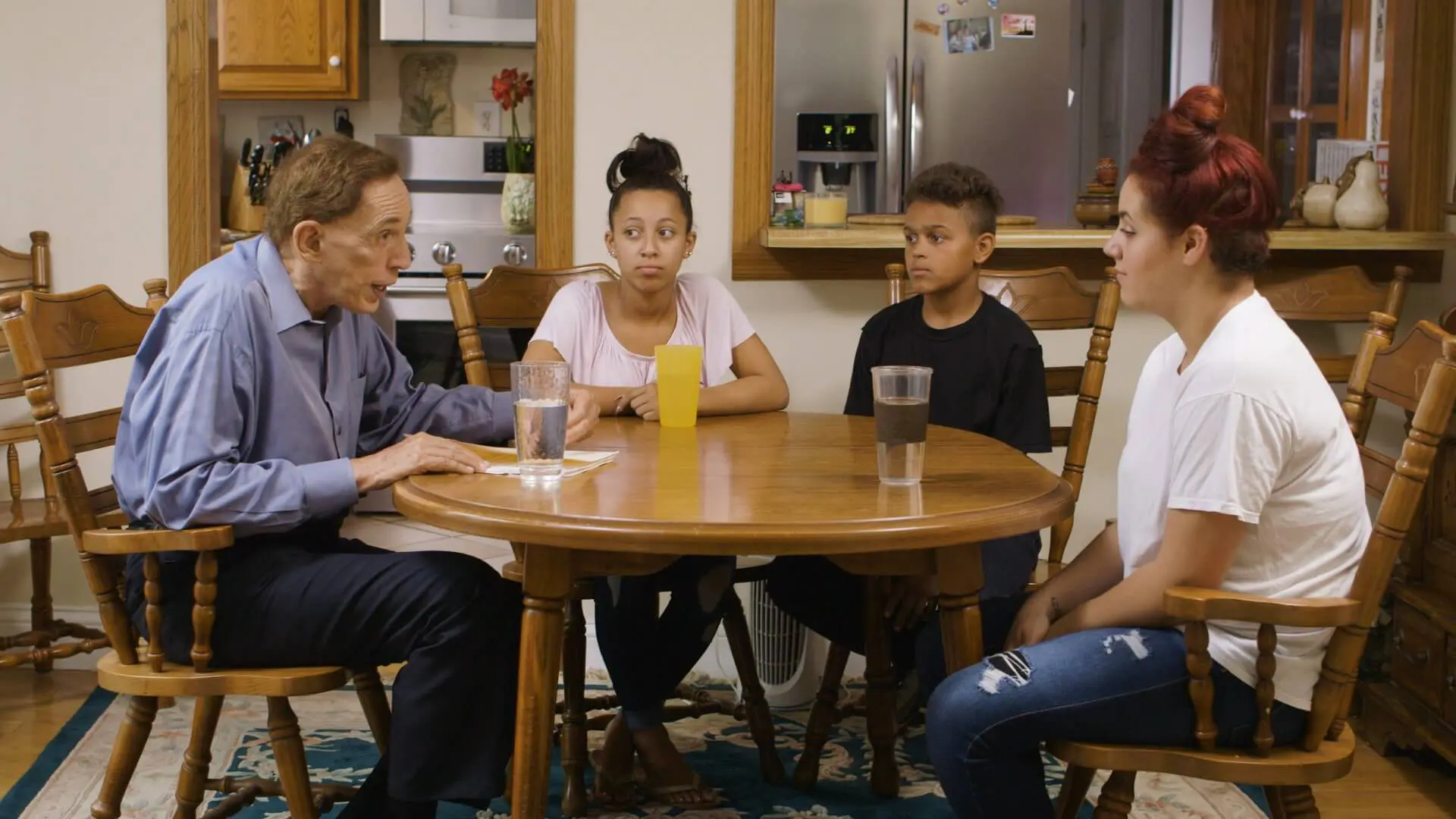
If a company’s product or service has injured you or a loved one, you may not be alone. Mass torts and class action lawsuits allow many people to sue a company for different reasons.
Sometimes the allegations include:
- Flawed product designs
- Defects in the manufacturing process
- Lack of appropriate information
- Products that didn’t meet state and federal guidelines.
Any of these could cause serious damage or harm, and it’s not your fault.
Current Recalls and Mass Tort Lawsuits
We’ve gathered the most recent class action lawsuits, product recalls, and mass torts happening in both state and federal courts because of manufacturing issues and product defects. If you believe you’ve been affected by any of the cases mentioned below, contact Bart Durham Injury Law today for a free consultation.
Ethylene Oxide (EtO) Linked to Cancer
The Sterilization Services of Tennessee facility at 2396 Florida Street in the Mallory Heights neighborhood of Memphis, Tennessee has exposed nearby residents to harmful levels of the human carcinogen “Ethylene Oxide” (EtO) for decades.
People who currently live or have lived within a 4-mile radius of the Sterilization Services of Tennessee facility could be eligible, and stronger claims may come from those who lived there in the 1980s.
Camp Lejeune Cancer Causing Chemicals
Did you or a family member serve on active duty or resided at Camp Lejeune Marine Corps base in North Carolina between August 1, 1953, and December 31, 1987? If so, you may be able to collect disability, health benefits, and financial compensation for several medical conditions linked to contaminated water. Learn more about how Bart Durham Law can help you get the compensation you deserve.
Roundup®
Roundup® is often used to kill weeds and maintain lawns. Regular use exposes you to dangerous chemicals that can cause Non-Hodgkin’s Lymphoma. Read more about the health concerns and joining the class action lawsuit.
Zantac
If you or someone you love has taken Zantac or any of the corresponding generic forms, you may be entitled to compensation. The manufacturers have recalled the drug due to links with deadly diseases. We have been going up against large corporations for years and are ready to fight for you.
Xarelto Injuries
Xarelto, also known as rivaroxaban, is a blood thinner. Patients were prescribed the drug when they had knee or hip replacement surgery. As a result, some suffered from internal bleeding, blood clots and more. Click to get the full list of side effects from using this medication.
Have you been injured? Consultations with Bart Durham are FREE and can lead to financial compensation.
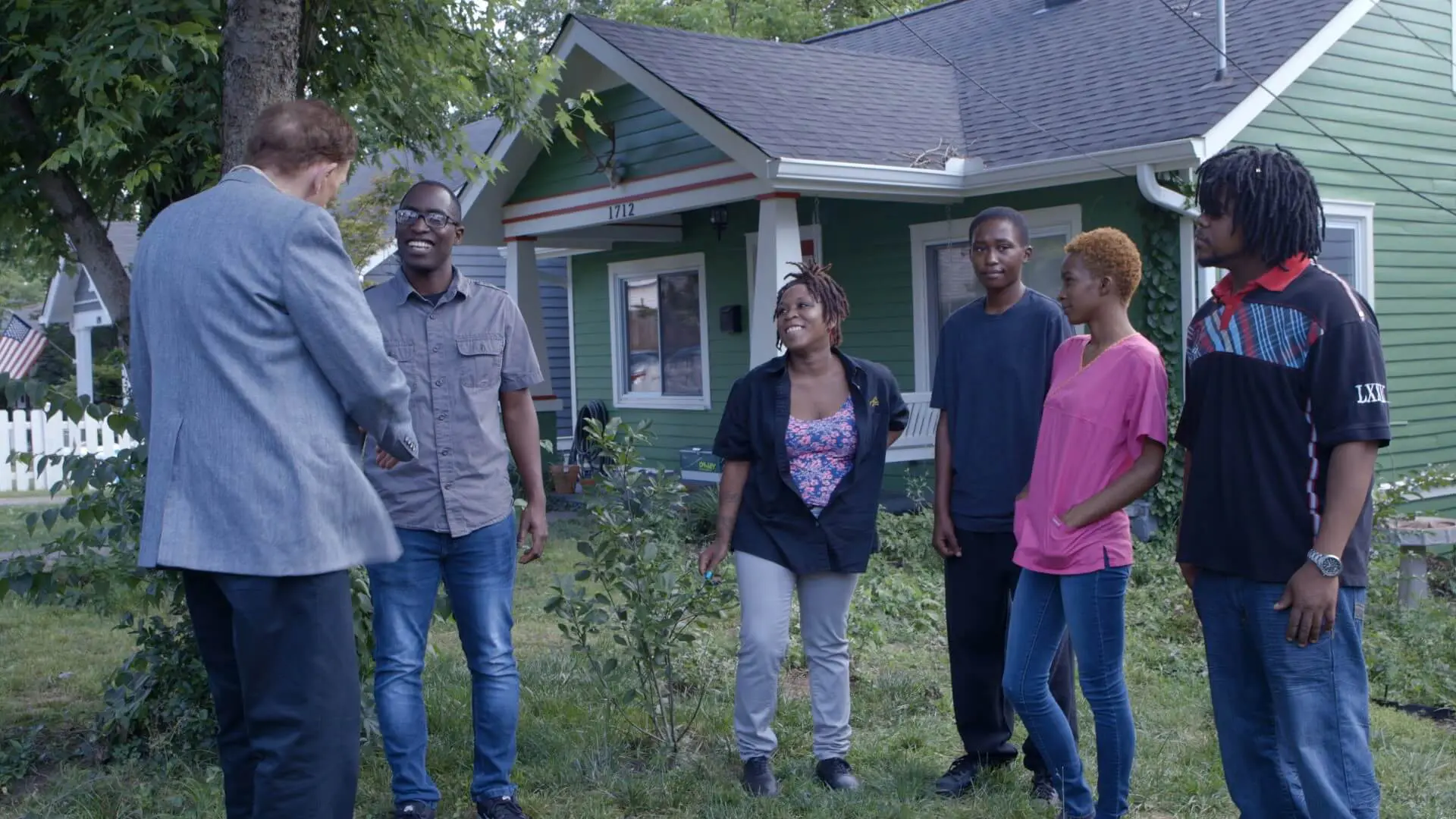
Does a Class Action Lawsuit Affect My Compensation?
Mass tort claims differ from other types of cases in that all of the plaintiffs split any financial compensation awarded in the case.
What Companies Might Have Product Recalls or Services?
Some examples of mass tort claims and class action lawsuits include, but are not limited to:
- Pharmaceutical drugs
- Medical devices
- Automobiles or automobile parts
- Children’s toys
- Home goods
- e-cigarettes
Additionally, people can file a claim against their employer over issues such as lack of overtime pay or exposure to harmful chemicals.
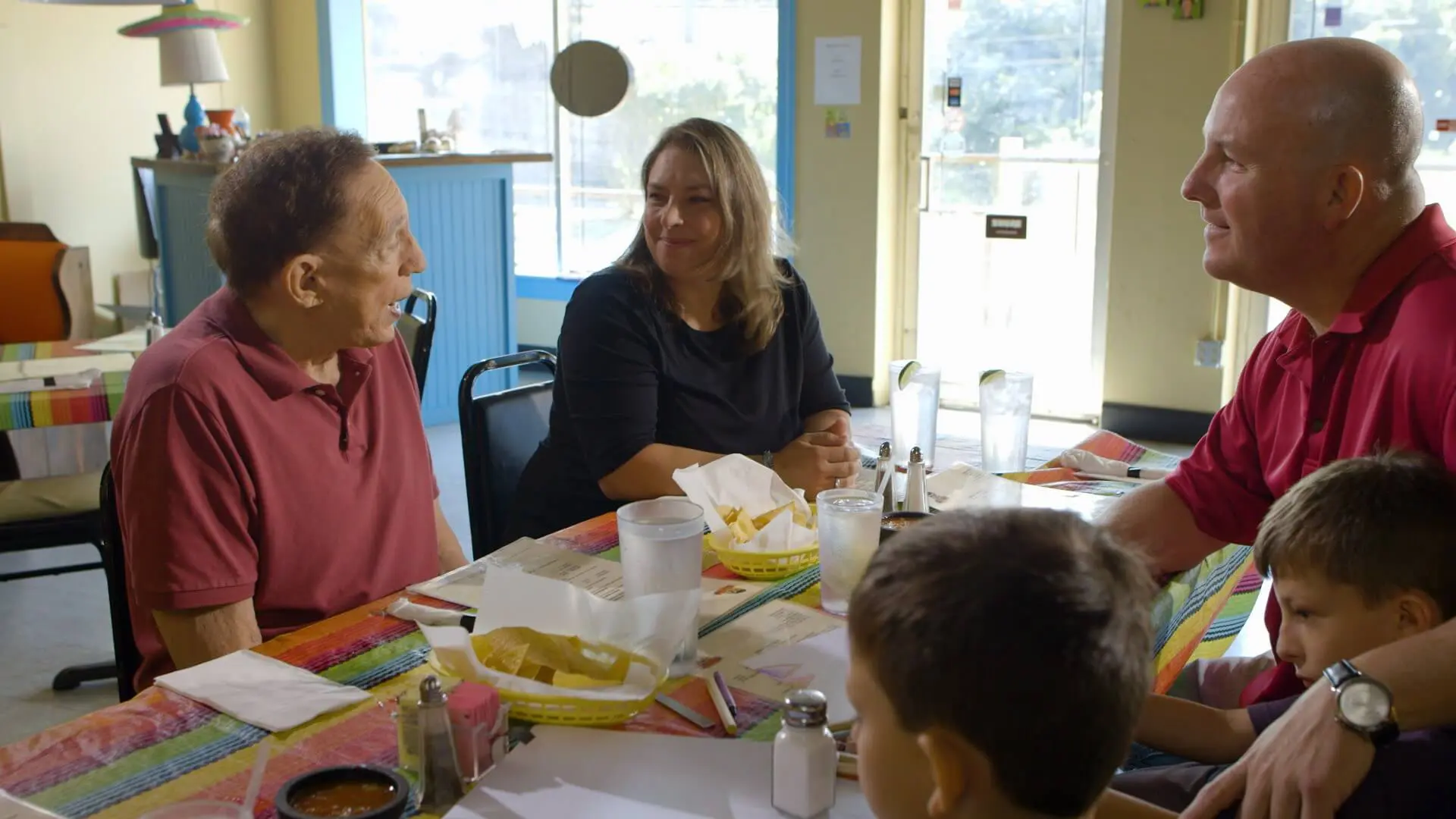
How Do I Join a Mass Tort?
The first thing you need to do is confirm you have a case. We are dedicated to protecting your rights. Injuries from product defects, recalls, or manufacturing issues are not acceptable. You deserve compensation for your loss. We’re here to help.
Mass Tort Lawyers
Review our current Mass Torts and let us know if you have been personally affected. We offer free consultations that allow you to speak with a lawyer to confirm you have a case and to let you know how we are going to help!
REACH OUT TODAY!
If you have been injured due to another’s actions, you do not need to go through the legal process on your own. Call us at 800-844-1712 to schedule a free initial consultation, or you can complete our online form.